Ingeniería Eléctrica junto a la fábrica de capacitores de media tensión de la mano de Leyden.
Ver Glosario de siglas
• ANSI: American National Standards Institute (Instituto Nacional Estadounidense de Normas)
• IEC: International Electrotechnical Commission (Comisión Electrotécnica Internacional)
• IEEE: Institute of Electrical and Electronics Engineers (Instituto de Ingenieros Eléctricos y Electrónicos)
• IRAM: Instituto Argentino de Certificación y Normalización
• NBR: Norma Brasileira (Norma Brasilera)
• OAA: Organismo Argentino de Acreditación
Un recorrido por la nueva planta de Leyden fue la excusa ideal para que “Ingeniería Eléctrica”, a través de Alejandra Bocchio y Jorge Menéndez, fuera testigo del proceso de fabricación y ensayo de capacitores de media y alta tensión.
Con el aval de Guillermo Bianchi, el presidente, fue el gerente de ingeniería, Daniel Gómez, quien ofició de guía. Su relevo en el laboratorio fue Damián Simkin, responsable de calidad.
Tres sectores tiene la planta: fabricación propiamente dicha, armado de bancos de media tensión y laboratorio. Cuatro, si se cuentan también los depósitos. Hay novedades en todos ellos: más espacio, mejor comunicación, más orden, más máquinas, todo bien valorado por una empresa que se dedica a la fabricación desde sus inicios, allá por 1943, cuando en un contexto de posguerras europeas se necesitaba reemplazar pequeños capacitores en la industria automotriz. Hoy en día es el único fabricante nacional que opera con altas tensiones en todo lo que a calidad de energía se refiere.
Cualquier capacitor está formado principalmente por un electrodo y un aislante. Las materias primas, que se ven en grandes cantidades ordenadas en pallets, son las siguientes: como dieléctrico, un film de polipropileno proveniente de Francia y como electrodo, folios de aluminio de uso eléctrico.
Con el aval de Guillermo Bianchi, el presidente, fue el gerente de ingeniería, Daniel Gómez, quien ofició de guía. Su relevo en el laboratorio fue Damián Simkin, responsable de calidad.
Tres sectores tiene la planta: fabricación propiamente dicha, armado de bancos de media tensión y laboratorio. Cuatro, si se cuentan también los depósitos. Hay novedades en todos ellos: más espacio, mejor comunicación, más orden, más máquinas, todo bien valorado por una empresa que se dedica a la fabricación desde sus inicios, allá por 1943, cuando en un contexto de posguerras europeas se necesitaba reemplazar pequeños capacitores en la industria automotriz. Hoy en día es el único fabricante nacional que opera con altas tensiones en todo lo que a calidad de energía se refiere.
Cualquier capacitor está formado principalmente por un electrodo y un aislante. Las materias primas, que se ven en grandes cantidades ordenadas en pallets, son las siguientes: como dieléctrico, un film de polipropileno proveniente de Francia y como electrodo, folios de aluminio de uso eléctrico.
Paso a paso
El proceso comienza en la sala de bobinado en donde se fabrica el primer elemento capacitivo. Se trata de una sala limpia presurizada puesto que opera con aluminio de espesores extremadamente delgados, medidos en micrones, que deberá conservar su pureza si recibirá altos voltajes. Es quizá esta la parte más delicada de la fabricación, tanto como la impregnación posterior.
El operario coloca el material sobre el buje de la bobinadora y enrolla el largo especificado en el diseño. Luego encima los rollos. Cada pila terminará formando un capacitor. Pilas de rollos de aluminio aplastadas por una prensa es el resultado de esta primera sala.
Antes de pasar a la siguiente, se llevan a cabo algunas pruebas como medición de capacitancia individual, revisión de espesores, aplicación de tensión continua, pesaje, etc.
En la sala de conexionado, los elementos capacitivos se colocan en dos prensas. Primero se apilan en función de series y paralelos, luego se les colocan todos los elementos adicionales, por ejemplo, los fusibles internos (en caso de que lo pidan). Y así preparados pasan al conexionado propiamente dicho: soldadura de cada elemento capacitivo.
Es en este momento cuando se les colocan los aislantes celulósicos, cartones y papeles de uso eléctrico provenientes de Alemania, para el aislamiento entre partes con tensión. El voltaje que deben soportar estos equipos es de 13,2 y 38 kV.
Los controles correspondientes a esta etapa son las mediciones de capacitancia, el pesaje de la bobina, medición de capacitancia en seco.
El resultado es una especie de paquete plegado de forma tal para que pueda entrar en una caja prismática, una caja de acero inoxidable con descargadores de sobretensión envueltos en porcelanas de uso eléctrico (porosidad nula) como tapa. La conexión final de la caja con el capacitivo se realiza en la sala de armado, donde también se suelda la tapa.
La etapa siguiente es la impregnación. Hasta aquí, todos los procesos se realizaron en seco, ahora, entra a jugar el aceite.
Tres autoclaves llevan adelante el proceso, primero, de precalentamiento, a fin de eliminar toda la humedad que tienen los aislantes celulósicos, papeles y cartones. Luego se genera el vacío acordado en el diseño y se enfría nuevamente. Recién entonces, ingresa el aceite. Una vez que las cajas se llenan, se deja un tiempo de reposo, se sueldan la tapas de impregnación y pasan al horno de curado. Ya soldadas y sin fuga de impregnantes, las cajas pasan a la verificación de estanqueidad, primer ensayo de rutina: se someten a temperaturas elevadas para detectar poros en las soldaduras.
El operario coloca el material sobre el buje de la bobinadora y enrolla el largo especificado en el diseño. Luego encima los rollos. Cada pila terminará formando un capacitor. Pilas de rollos de aluminio aplastadas por una prensa es el resultado de esta primera sala.
Antes de pasar a la siguiente, se llevan a cabo algunas pruebas como medición de capacitancia individual, revisión de espesores, aplicación de tensión continua, pesaje, etc.
En la sala de conexionado, los elementos capacitivos se colocan en dos prensas. Primero se apilan en función de series y paralelos, luego se les colocan todos los elementos adicionales, por ejemplo, los fusibles internos (en caso de que lo pidan). Y así preparados pasan al conexionado propiamente dicho: soldadura de cada elemento capacitivo.
Es en este momento cuando se les colocan los aislantes celulósicos, cartones y papeles de uso eléctrico provenientes de Alemania, para el aislamiento entre partes con tensión. El voltaje que deben soportar estos equipos es de 13,2 y 38 kV.
Los controles correspondientes a esta etapa son las mediciones de capacitancia, el pesaje de la bobina, medición de capacitancia en seco.
El resultado es una especie de paquete plegado de forma tal para que pueda entrar en una caja prismática, una caja de acero inoxidable con descargadores de sobretensión envueltos en porcelanas de uso eléctrico (porosidad nula) como tapa. La conexión final de la caja con el capacitivo se realiza en la sala de armado, donde también se suelda la tapa.
La etapa siguiente es la impregnación. Hasta aquí, todos los procesos se realizaron en seco, ahora, entra a jugar el aceite.
Tres autoclaves llevan adelante el proceso, primero, de precalentamiento, a fin de eliminar toda la humedad que tienen los aislantes celulósicos, papeles y cartones. Luego se genera el vacío acordado en el diseño y se enfría nuevamente. Recién entonces, ingresa el aceite. Una vez que las cajas se llenan, se deja un tiempo de reposo, se sueldan la tapas de impregnación y pasan al horno de curado. Ya soldadas y sin fuga de impregnantes, las cajas pasan a la verificación de estanqueidad, primer ensayo de rutina: se someten a temperaturas elevadas para detectar poros en las soldaduras.
El nuevo laboratorio
El nuevo laboratorio de Leyden está acreditado por norma 17025 ante el OAA por lo cual cualquier ensayo que realice puede ser reconocido a nivel mundial. Sin dudas, uno de los grandes hitos que se suman a la historia de la marca.
Está equipado para hacer todos los ensayos de rutina y todos los ensayos de tipo que piden las normas IEC, ANSI, IEEE, IRAM, NBR. La totalidad de los equipos fabricados pasan por sus ensayos de rutina correspondientes. En caso de que el cliente lo solicite, también se hacen los ensayos de tipo. Los clientes también pueden presenciar los ensayos.
Ensayo de masa, de bornes, entre bornes, descarga entre fusibles, medición de capacidad, medición de tangente de pérdida a tensión nominal, etc. todo eso se realiza a un aproximado de treinta capacitores por día, trabajando de forma tranquila.
Llaman la atención la nueva sala de control, el capacitor patrón, el generador de impulsos hasta 300 kV, la inductancia variable y demás equipos, todos nuevos. La mudanza de Leyden le dio al laboratorio un 300% más de capacidad, con lo cual sumó maquinaria para realizar pruebas que antes no podía.
Está equipado para hacer todos los ensayos de rutina y todos los ensayos de tipo que piden las normas IEC, ANSI, IEEE, IRAM, NBR. La totalidad de los equipos fabricados pasan por sus ensayos de rutina correspondientes. En caso de que el cliente lo solicite, también se hacen los ensayos de tipo. Los clientes también pueden presenciar los ensayos.
Ensayo de masa, de bornes, entre bornes, descarga entre fusibles, medición de capacidad, medición de tangente de pérdida a tensión nominal, etc. todo eso se realiza a un aproximado de treinta capacitores por día, trabajando de forma tranquila.
Llaman la atención la nueva sala de control, el capacitor patrón, el generador de impulsos hasta 300 kV, la inductancia variable y demás equipos, todos nuevos. La mudanza de Leyden le dio al laboratorio un 300% más de capacidad, con lo cual sumó maquinaria para realizar pruebas que antes no podía.
Pintura y últimos retoques
En Leyden no hay procesos tercerizados. Del laboratorio, cada capacitor pasa al sector de pintado, donde recibe una base de epoxi y una terminación de poliuretano que los hace aptos para la intemperie. La caja se pinta del color gris estándar de productos eléctricos: RAL 7030.
Por último, se le suman las etiquetas y la placa de características.
Cada capacitor se puede vender individualmente o puede formar parte de un banco de media tensión que se puede proveer con su propio tablero.
Por último, se le suman las etiquetas y la placa de características.
Cada capacitor se puede vender individualmente o puede formar parte de un banco de media tensión que se puede proveer con su propio tablero.
Palabras finales
La trazabilidad se logra a través del seguimiento pormenorizado: desde los diseños ingenieriles, hasta los datos que se deben tomar en cada una de las etapas de fabricación, todo queda asentado como información del producto que recorrerá toda la línea de producción.
La calidad es hija de las materias utilizadas y de los procesos que se llevan a cabo con tanto esmero. Amén de los ensayos de laboratorio, cada etapa realiza controles obligatorios, por ejemplo, de capacitancia.
Entre doscientos y trescientos capacitores de media tensión por mes salen de la fábrica de Leyden. El proceso comienza con las materias primas más básicas y culmina con equipos tecnológicos que evidencian un alto nivel industrial.
La calidad es hija de las materias utilizadas y de los procesos que se llevan a cabo con tanto esmero. Amén de los ensayos de laboratorio, cada etapa realiza controles obligatorios, por ejemplo, de capacitancia.
Entre doscientos y trescientos capacitores de media tensión por mes salen de la fábrica de Leyden. El proceso comienza con las materias primas más básicas y culmina con equipos tecnológicos que evidencian un alto nivel industrial.
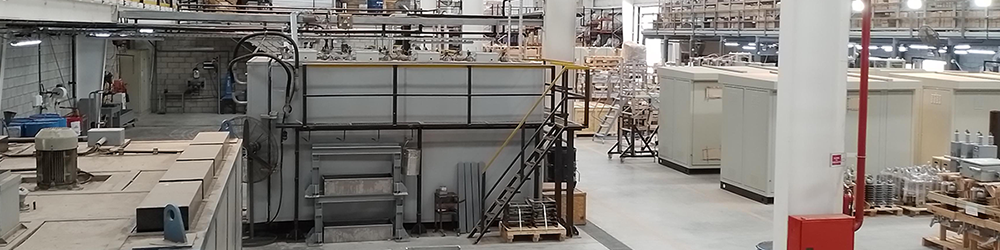
Por Leyden
Fuente: entrevista en la empresa
Todas las publicaciones de:
Publicado en:
Número:
Mes:
Año: